FUJIFILM Cut Loose Thanks to Razor-sharp Planning Tool
The original version of this article was published on the CQM website. CQM is an AIMMS Implementation partner.
Did you know that many magazines, newspapers, and even the packaging of your favorite breakfast cereal start out as part of a 7km-long roll of aluminum? A photosensitive coating is then applied to the roll before it is cut to size and the printer can get to work. FUJIFILM in Tilburg makes these so-called offset plates for the graphics industry. Coated aluminum sheets are expensive to produce, so Logistics Manager Maurice Janssen and Logistics Supervisor Bart Verhoeven were looking to optimize the process in order to reduce cutting loss, and therefore costs, during production. To learn more about the project, we rolled out the red carpet for the two managers — admittedly not a 7km carpet, but you can’t have everything…
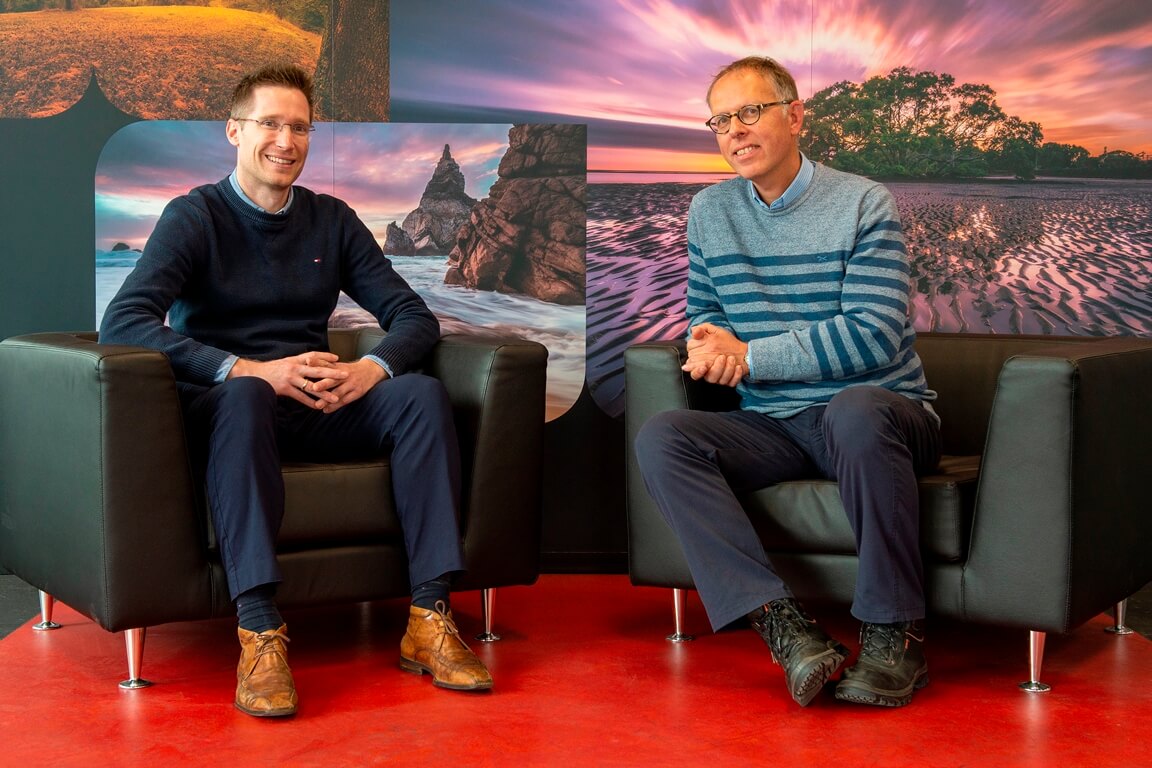
Simplifying a complex process
“We actually had two issues,” says Bart. “We wanted to optimize the work process itself and the planning system we used. In our factory, we process aluminum rolls, to which we apply a coating layer before cutting the roll into smaller, so-called ‘offset plates’. The original aluminum rollers vary from 7 to 14 km long! They have to be cut into various different shapes and sizes to match the size, for example, of a newspaper or magazine’s blueprint at the printer.
As you can imagine, with plate sizes and customer requirements varying so much, considerable cutting loss can occur during this process. It’s extremely costly and very environmentally unfriendly to throw any part of these coated aluminum sheets away. So we obviously want to minimize cutting loss. CQM recommended a customized system that would give us more room to optimize our work process. It meant building a new planning system from scratch, but we now have more freedom of choice than before.”
“CQM was actually the only partner who could help us with this,” adds Maurice. “Most parties find our processes complex and have difficulty understanding them. We’re often told what we do is ‘rocket science’. And if that’s so, where better to go than CQM? They’re smart cookies who have the ability to translate our processes into models and don’t shy away from customization.”
Less cutting loss and 4 times faster
“Every time we plan a batch,” explains Bart, “we’re effectively piecing together a new puzzle to deliver the products requested: we have different product types for magazines, newspapers, and packaging material, and have to take into account a variety of formats and print runs. To combine all these factors with as little cutting loss as possible, we previously used a complicated Excel program. It worked, but it was very time-consuming.”
“When an order came in, there was a good month of puzzling away before we could actually start producing the offset plates,” explains Maurice. “With the help of CQM’s new tool, this planning process has been reduced to a week. That not only saves time, but also significant costs. Partly because we no longer have to do the puzzling ourselves, but also because it’s done smarter with less cutting loss. As you can imagine, with such valuable raw materials, even a small percentage reduction in cutting loss delivers considerable savings.”
More Sustainable work process
“At FUJIFILM, sustainability is one of our highest priorities,” says Maurice. “And as we now have less cutting loss, we throw away less aluminum and therefore have a smaller impact on the environment. We also wanted to have less intermediate stock. We first planned the coating process separately, then looked at whether it was sufficient to produce an end product. Having clarity about the puzzle beforehand can have a significant positive impact on your intermediate stock.”
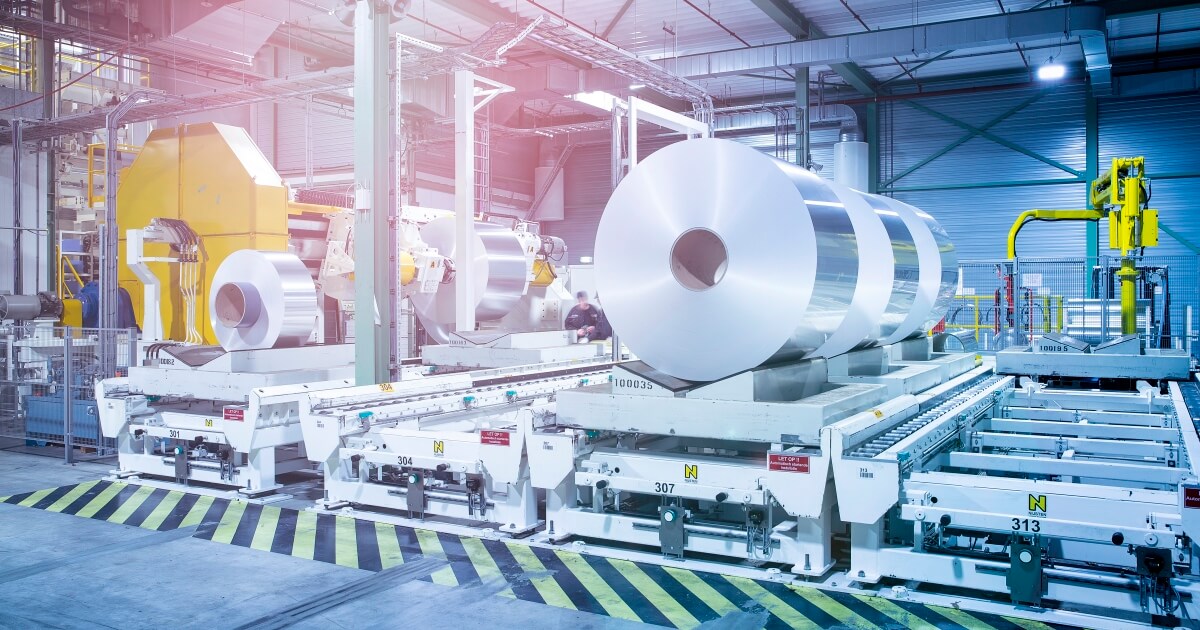
Dot on the horizon
“I’m very satisfied with the final result,” reflects Bart. “Our production process itself hasn’t speeded up, because our lines still work the same way; but the net output is far higher. It now literally gives us more. We now work much more efficiently than previously. It was really enjoyable working with CQM. Even though we at times strayed from the path or lost sight of that dot on the horizon, CQM always managed to get us back on course and keep us focused on the end-goal. Sometimes you get carried away, wanting to optimize everything; but trying to do too much is almost never effective.
“Plus the CQM staff are very approachable and accessible. They’re with us on a weekly basis, which makes them a real part of the team. This allows them to provide very specific advice and really dare to say when something isn’t going to work. They take your hand to guide you through things really well, which is great. And I’ve been really impressed by how quickly they mastered our production process and then translated that into an efficient, workable mathematical model.”
The circle is complete
“To optimize our planning process,” concludes Maurice, “CQM had to take into account a lot of different parameters and exceptions. Some companies come with a system that they stick to and something then has to be built around it, as it were. At CQM, it’s the other way around: your work process forms the basis and the system is designed around that, which means that only relevant functionalities are created. For FUJIFILM, they did this in collaboration with AIMMS.”
“They’re good people, who look after a project right down to the last detail. And that includes the aftercare: a call a few weeks after completion, chocolates for Sinterklaas… I really value that sort of thing. Chocolates for which we did the packaging. With minimal cutting loss, of course, thanks to CQM — the circle is complete!”
Jacob Jan, the CQM consultant who worked on this project said, “What surprised me was the wide variety of product sizes printers expect from FUJIFILM. But when you stand in front of a magazine rack and see that almost everything differs in size, it makes sense. With our mathematical optimization, we initially focused on reducing the cutting loss. Which products are you going to combine and which cutting patterns will you apply to them? There are so many variations that you can’t expect a human to have an oversight of this. The value of the product meant that FUJIFILM had long since grabbed any quick wins (and more) to be made in the process. To then take things a step further isn’t easy. We also investigated the feasibility of the plan because, in addition to any hard machine restrictions, the plan also has to be practically executable and efficient for the people on the work floor.”
Learn more about developing custom planning apps with the AIMMS low-code platform.